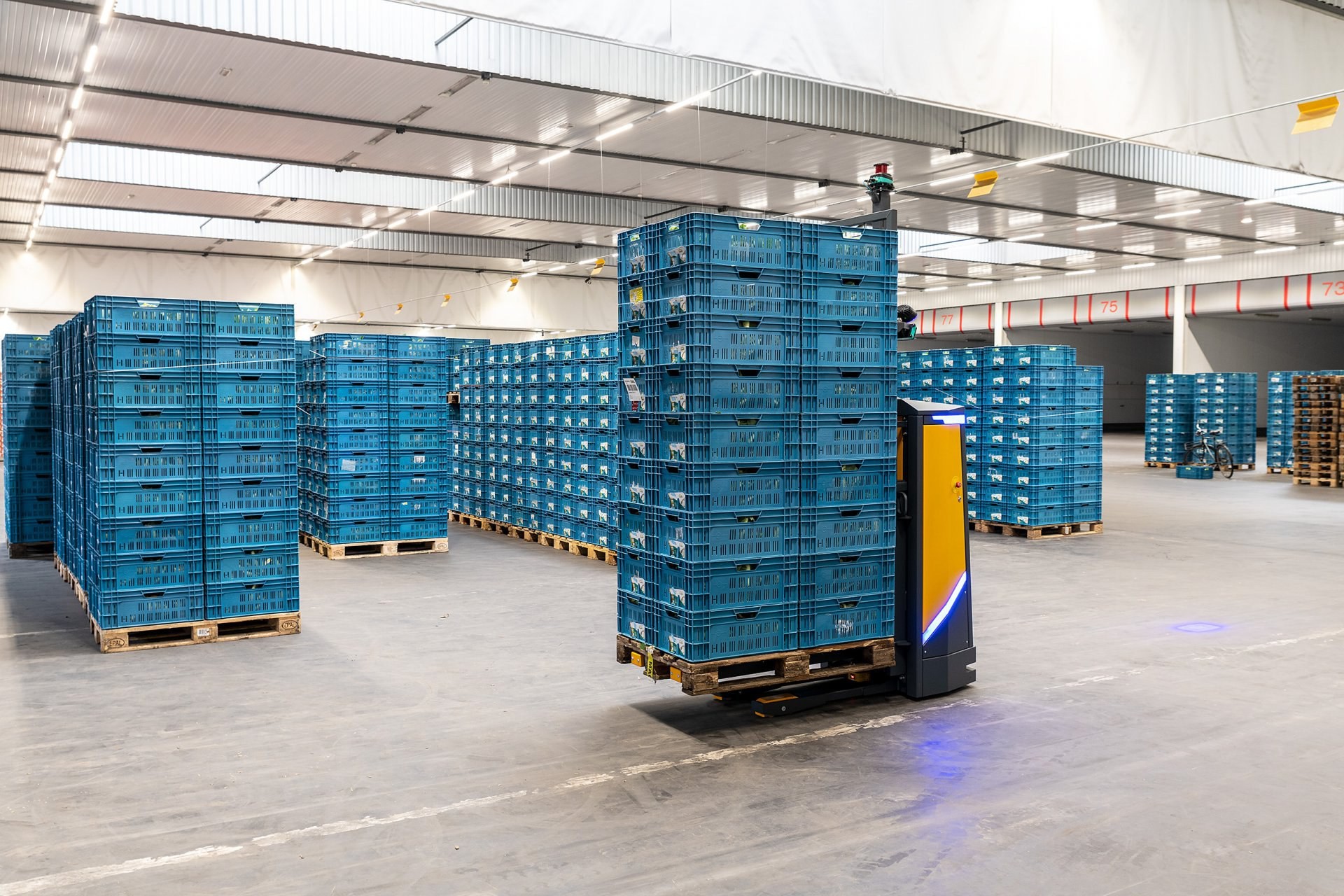
Insights
October 19, 2024
Automation and Robotics in Warehousing: How AGVs and Robotics Are Transforming the Logistics Industry
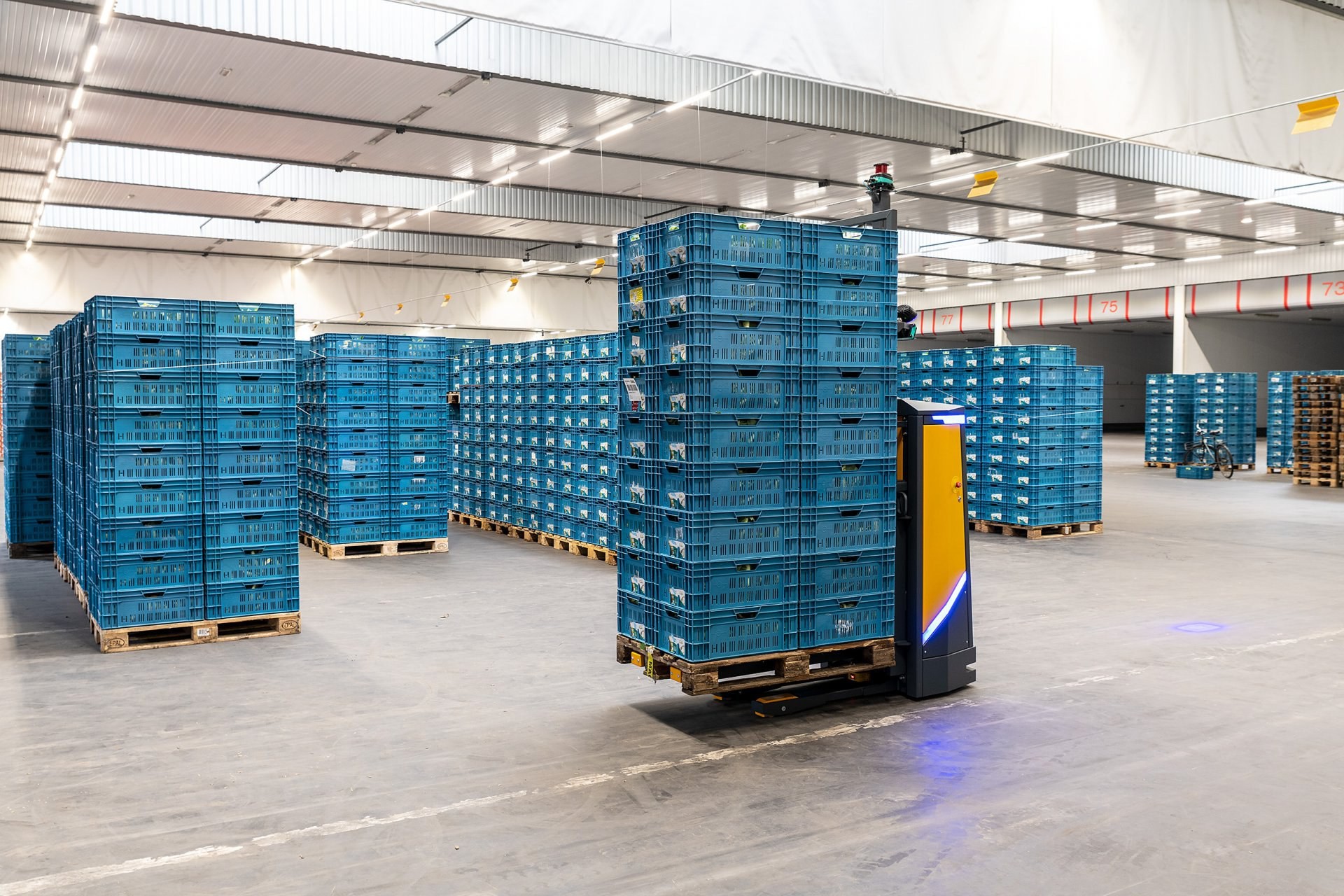
Insights
October 19, 2024
Automation and Robotics in Warehousing: How AGVs and Robotics Are Transforming the Logistics Industry
Warehousing automation is transforming logistics with technologies like AGVs, robotics, and AS/RS. Learn how these solutions address labor shortages, enhance efficiency, and prepare companies for the future.
As the logistics industry faces ongoing labor shortages and rising demand, companies are increasingly turning to automation and robotics to enhance warehouse operations. Automation technologies, such as automated guided vehicles (AGVs), robotics, and automated storage and retrieval systems (AS/RS), enable companies to manage higher volumes with fewer workers while maintaining operational speed and accuracy. These technologies not only optimize processes but also help businesses meet evolving customer expectations for rapid delivery and error-free order fulfillment.
This article explores the role of automation and robotics in warehousing, detailing the benefits, challenges, and future trends in this transformative area of logistics.
The Need for Automation in Warehousing
1.1 Combating Labor Shortages
The logistics sector is grappling with a significant labor shortage that is impacting warehousing operations:
Labor Market Challenges:
The logistics industry has struggled to attract and retain workers due to the physically demanding nature of warehouse jobs and competitive hiring pressures.
High turnover rates and an aging workforce further exacerbate the challenge of filling warehousing positions, especially during peak seasons.
Increasing Wage Costs:
Wage inflation and competitive hiring incentives are driving up labor costs, prompting companies to seek cost-effective automation solutions.
Automation reduces dependency on manual labor, helping to mitigate the financial impact of rising wages.
1.2 Managing Higher Volumes and Customer Expectations
Automation is not only a response to labor shortages but also a solution to meet the demands of a rapidly evolving market:
Growth of E-commerce:
The surge in e-commerce has increased pressure on warehouses to handle larger volumes of orders with shorter fulfillment times.
Seasonal peaks, such as Black Friday and holiday shopping, demand flexible and scalable warehouse operations to meet heightened customer expectations.
Need for Speed and Accuracy:
Customers expect same-day or next-day delivery, making speed and precision critical factors in order fulfillment.
Automated systems enhance efficiency by performing repetitive tasks more quickly and accurately than human workers.
Key Automation Technologies in Warehousing
2.1 Automated Guided Vehicles (AGVs)
AGVs are among the most widely used automation technologies in warehouses, offering flexibility and efficiency in material handling:
Overview of AGVs:
AGVs are self-driving vehicles that navigate warehouse floors using sensors, cameras, and pre-programmed routes to transport goods.
These vehicles can operate autonomously or be programmed to follow designated paths, reducing the need for human intervention.
Types of AGVs in Warehousing:
Tugger AGVs: Designed to pull carts or trailers, often used for moving large quantities of goods between different areas.
Unit Load AGVs: Suitable for transporting pallets, bins, or containers; ideal for high-throughput environments.
Forklift AGVs: Automate the lifting and stacking of pallets, offering a safer alternative to traditional manual forklifts.
Benefits of AGVs:
Reduced labor costs: AGVs automate repetitive tasks, allowing companies to reallocate workers to more complex roles.
Increased safety: Automated vehicles reduce the risk of workplace accidents associated with manual material handling.
Scalability: AGVs can be easily added or removed based on demand, making them suitable for warehouses of various sizes.
2.2 Robotics and Robotic Process Automation (RPA)
Robotics and RPA are transforming warehousing by automating complex and repetitive tasks:
Types of Robotics Used in Warehousing:
Collaborative robots (cobots): Work alongside human workers to assist with tasks such as order picking, packing, and sorting.
Sorting robots: Used to pick and place items in the correct locations, streamlining sorting processes in distribution centers.
Palletizing robots: Automate the stacking and organizing of goods on pallets, increasing efficiency in loading and unloading.
Applications of RPA in Warehousing:
Automating data entry: RPA can handle repetitive administrative tasks such as inventory tracking, order processing, and shipment scheduling.
Enhancing workflow efficiency: RPA helps streamline warehouse management processes by integrating with existing warehouse management systems (WMS).
2.3 Automated Storage and Retrieval Systems (AS/RS)
AS/RS technology is essential for maximizing warehouse storage efficiency and optimizing inventory management:
What Is AS/RS?:
AS/RS are computer-controlled systems that automatically place and retrieve goods from storage locations. These systems are often used in conjunction with other automation technologies for a fully integrated approach.
Types of AS/RS:
Mini-load AS/RS: Designed for handling smaller items such as boxes, bins, and cartons.
Unit-load AS/RS: Suitable for storing large and heavy items, typically on pallets.
Shuttle systems: Use automated shuttles to move goods within high-density storage racks, providing quick access to items.
Advantages of AS/RS:
Increased storage capacity: AS/RS allows for vertical stacking, optimizing the use of available space and enabling high-density storage configurations.
Faster retrieval times: Automated systems reduce the time needed to locate and retrieve items, improving order fulfillment speed.
Benefits of Automation and Robotics in Warehousing
3.1 Increased Efficiency and Productivity
Automation allows warehouses to operate more efficiently, even with fewer workers:
Optimizing Material Handling:
Automated systems streamline the movement of goods throughout the warehouse, reducing handling times and minimizing bottlenecks.
Consistent Performance:
Unlike human workers, machines do not experience fatigue or performance fluctuations, ensuring a steady rate of productivity throughout the day.
3.2 Enhanced Accuracy and Reduced Errors
Automation improves order accuracy and reduces the risk of mistakes:
Minimizing Human Error:
Automated picking and sorting systems are programmed to perform tasks precisely, reducing the likelihood of errors.
Improved Quality Control:
Robots can be used to inspect products for defects or discrepancies, ensuring consistent quality in order fulfillment.
3.3 Better Use of Space
Automation helps companies optimize warehouse layouts and maximize storage capacity:
Maximizing Storage Capacity:
AS/RS and other high-density storage solutions make better use of vertical space, allowing warehouses to store more inventory in a smaller footprint.
Flexible Warehouse Layouts:
Automated systems enable more adaptable warehouse designs, allowing facilities to be quickly reconfigured in response to changing operational needs.
Challenges and Considerations in Implementing Automation
4.1 High Initial Investment Costs
The cost of automation is a significant barrier for many companies:
Capital Expenditure for Equipment:
The upfront cost of acquiring AGVs, robotics, and AS/RS can be substantial, particularly for small and medium-sized businesses.
Infrastructure Upgrades:
Existing warehouses may require upgrades to support automation, such as installing power lines, enhancing network connectivity, or reinforcing floors.
4.2 Integration with Existing Systems
Integrating new automation technologies with legacy systems can be challenging:
Compatibility Issues:
New automation solutions may not be easily compatible with older warehouse management systems (WMS), requiring customization or upgrades.
Training Requirements:
Employees need to be trained to operate, monitor, and maintain the new automated systems, which may involve a learning curve.
4.3 Workforce Implications
While automation can reduce the need for manual labor, it also affects the workforce:
Impact on Employment:
Concerns about job displacement arise as manual tasks are automated. Companies need to manage the transition carefully to avoid negative impacts on employees.
Upskilling Opportunities:
Automation creates new roles in areas such as robot maintenance, programming, and data analysis. Companies should invest in training programs to help workers develop these skills.
Future Trends in Warehouse Automation
5.1 Increased Adoption of AI and Machine Learning
AI and machine learning will continue to drive advancements in warehouse automation:
AI-Powered Predictive Analytics:
AI can be used for demand forecasting, optimizing inventory levels, and conducting predictive maintenance on equipment.
Robots with Advanced AI Capabilities:
Robots will increasingly be equipped with AI that allows them to learn, adapt, and perform more complex tasks.
5.2 Expansion of Collaborative Robotics
The use of collaborative robots (cobots) in warehouses is expected to grow:
Rise of Cobots:
More warehouses will integrate cobots to assist human workers with tasks such as lifting, picking, and sorting, especially in environments where human dexterity is required.
Human-Robot Collaboration Models:
New collaboration models will emerge, leveraging the strengths of both human workers and robots for more efficient operations.
5.3 Growth in Micro-Fulfillment Centers
Micro-fulfillment centers will increasingly rely on automation to meet urban logistics needs:
Small-Scale Automation for Urban Logistics:
Micro-fulfillment centers will adopt automation to cater to last-mile delivery demands and enable same-day or next-day shipping.
Use of Robotics in Small Warehouses:
Even smaller, decentralized warehouses will incorporate robotics to optimize space utilization and speed up operations.
Conclusion
Automation and robotics are revolutionizing warehousing by addressing labor shortages, enhancing operational efficiency, and meeting evolving customer expectations. Technologies like AGVs, robotics, and AS/RS are helping companies handle higher volumes with greater speed and accuracy while optimizing the use of warehouse space. Although the implementation of automation involves challenges, such as high costs and integration complexities, the long-term benefits of increased productivity and accuracy make it a worthwhile investment. As AI, collaborative robotics, and micro-fulfillment centers continue to shape the future of warehouse automation, companies that embrace these technologies will be well-positioned for success.
Key Takeaways:
Automation provides significant gains in efficiency, accuracy, and space optimization.
Initial costs and integration challenges should be carefully managed to maximize ROI.
Future trends in AI and collaborative robotics will drive the next wave of warehouse automation advancements.
Call to Action (CTA): Share your experiences with warehouse automation and let us know how your organization is leveraging robotics and automation to improve efficiency.
As the logistics industry faces ongoing labor shortages and rising demand, companies are increasingly turning to automation and robotics to enhance warehouse operations. Automation technologies, such as automated guided vehicles (AGVs), robotics, and automated storage and retrieval systems (AS/RS), enable companies to manage higher volumes with fewer workers while maintaining operational speed and accuracy. These technologies not only optimize processes but also help businesses meet evolving customer expectations for rapid delivery and error-free order fulfillment.
This article explores the role of automation and robotics in warehousing, detailing the benefits, challenges, and future trends in this transformative area of logistics.
The Need for Automation in Warehousing
1.1 Combating Labor Shortages
The logistics sector is grappling with a significant labor shortage that is impacting warehousing operations:
Labor Market Challenges:
The logistics industry has struggled to attract and retain workers due to the physically demanding nature of warehouse jobs and competitive hiring pressures.
High turnover rates and an aging workforce further exacerbate the challenge of filling warehousing positions, especially during peak seasons.
Increasing Wage Costs:
Wage inflation and competitive hiring incentives are driving up labor costs, prompting companies to seek cost-effective automation solutions.
Automation reduces dependency on manual labor, helping to mitigate the financial impact of rising wages.
1.2 Managing Higher Volumes and Customer Expectations
Automation is not only a response to labor shortages but also a solution to meet the demands of a rapidly evolving market:
Growth of E-commerce:
The surge in e-commerce has increased pressure on warehouses to handle larger volumes of orders with shorter fulfillment times.
Seasonal peaks, such as Black Friday and holiday shopping, demand flexible and scalable warehouse operations to meet heightened customer expectations.
Need for Speed and Accuracy:
Customers expect same-day or next-day delivery, making speed and precision critical factors in order fulfillment.
Automated systems enhance efficiency by performing repetitive tasks more quickly and accurately than human workers.
Key Automation Technologies in Warehousing
2.1 Automated Guided Vehicles (AGVs)
AGVs are among the most widely used automation technologies in warehouses, offering flexibility and efficiency in material handling:
Overview of AGVs:
AGVs are self-driving vehicles that navigate warehouse floors using sensors, cameras, and pre-programmed routes to transport goods.
These vehicles can operate autonomously or be programmed to follow designated paths, reducing the need for human intervention.
Types of AGVs in Warehousing:
Tugger AGVs: Designed to pull carts or trailers, often used for moving large quantities of goods between different areas.
Unit Load AGVs: Suitable for transporting pallets, bins, or containers; ideal for high-throughput environments.
Forklift AGVs: Automate the lifting and stacking of pallets, offering a safer alternative to traditional manual forklifts.
Benefits of AGVs:
Reduced labor costs: AGVs automate repetitive tasks, allowing companies to reallocate workers to more complex roles.
Increased safety: Automated vehicles reduce the risk of workplace accidents associated with manual material handling.
Scalability: AGVs can be easily added or removed based on demand, making them suitable for warehouses of various sizes.
2.2 Robotics and Robotic Process Automation (RPA)
Robotics and RPA are transforming warehousing by automating complex and repetitive tasks:
Types of Robotics Used in Warehousing:
Collaborative robots (cobots): Work alongside human workers to assist with tasks such as order picking, packing, and sorting.
Sorting robots: Used to pick and place items in the correct locations, streamlining sorting processes in distribution centers.
Palletizing robots: Automate the stacking and organizing of goods on pallets, increasing efficiency in loading and unloading.
Applications of RPA in Warehousing:
Automating data entry: RPA can handle repetitive administrative tasks such as inventory tracking, order processing, and shipment scheduling.
Enhancing workflow efficiency: RPA helps streamline warehouse management processes by integrating with existing warehouse management systems (WMS).
2.3 Automated Storage and Retrieval Systems (AS/RS)
AS/RS technology is essential for maximizing warehouse storage efficiency and optimizing inventory management:
What Is AS/RS?:
AS/RS are computer-controlled systems that automatically place and retrieve goods from storage locations. These systems are often used in conjunction with other automation technologies for a fully integrated approach.
Types of AS/RS:
Mini-load AS/RS: Designed for handling smaller items such as boxes, bins, and cartons.
Unit-load AS/RS: Suitable for storing large and heavy items, typically on pallets.
Shuttle systems: Use automated shuttles to move goods within high-density storage racks, providing quick access to items.
Advantages of AS/RS:
Increased storage capacity: AS/RS allows for vertical stacking, optimizing the use of available space and enabling high-density storage configurations.
Faster retrieval times: Automated systems reduce the time needed to locate and retrieve items, improving order fulfillment speed.
Benefits of Automation and Robotics in Warehousing
3.1 Increased Efficiency and Productivity
Automation allows warehouses to operate more efficiently, even with fewer workers:
Optimizing Material Handling:
Automated systems streamline the movement of goods throughout the warehouse, reducing handling times and minimizing bottlenecks.
Consistent Performance:
Unlike human workers, machines do not experience fatigue or performance fluctuations, ensuring a steady rate of productivity throughout the day.
3.2 Enhanced Accuracy and Reduced Errors
Automation improves order accuracy and reduces the risk of mistakes:
Minimizing Human Error:
Automated picking and sorting systems are programmed to perform tasks precisely, reducing the likelihood of errors.
Improved Quality Control:
Robots can be used to inspect products for defects or discrepancies, ensuring consistent quality in order fulfillment.
3.3 Better Use of Space
Automation helps companies optimize warehouse layouts and maximize storage capacity:
Maximizing Storage Capacity:
AS/RS and other high-density storage solutions make better use of vertical space, allowing warehouses to store more inventory in a smaller footprint.
Flexible Warehouse Layouts:
Automated systems enable more adaptable warehouse designs, allowing facilities to be quickly reconfigured in response to changing operational needs.
Challenges and Considerations in Implementing Automation
4.1 High Initial Investment Costs
The cost of automation is a significant barrier for many companies:
Capital Expenditure for Equipment:
The upfront cost of acquiring AGVs, robotics, and AS/RS can be substantial, particularly for small and medium-sized businesses.
Infrastructure Upgrades:
Existing warehouses may require upgrades to support automation, such as installing power lines, enhancing network connectivity, or reinforcing floors.
4.2 Integration with Existing Systems
Integrating new automation technologies with legacy systems can be challenging:
Compatibility Issues:
New automation solutions may not be easily compatible with older warehouse management systems (WMS), requiring customization or upgrades.
Training Requirements:
Employees need to be trained to operate, monitor, and maintain the new automated systems, which may involve a learning curve.
4.3 Workforce Implications
While automation can reduce the need for manual labor, it also affects the workforce:
Impact on Employment:
Concerns about job displacement arise as manual tasks are automated. Companies need to manage the transition carefully to avoid negative impacts on employees.
Upskilling Opportunities:
Automation creates new roles in areas such as robot maintenance, programming, and data analysis. Companies should invest in training programs to help workers develop these skills.
Future Trends in Warehouse Automation
5.1 Increased Adoption of AI and Machine Learning
AI and machine learning will continue to drive advancements in warehouse automation:
AI-Powered Predictive Analytics:
AI can be used for demand forecasting, optimizing inventory levels, and conducting predictive maintenance on equipment.
Robots with Advanced AI Capabilities:
Robots will increasingly be equipped with AI that allows them to learn, adapt, and perform more complex tasks.
5.2 Expansion of Collaborative Robotics
The use of collaborative robots (cobots) in warehouses is expected to grow:
Rise of Cobots:
More warehouses will integrate cobots to assist human workers with tasks such as lifting, picking, and sorting, especially in environments where human dexterity is required.
Human-Robot Collaboration Models:
New collaboration models will emerge, leveraging the strengths of both human workers and robots for more efficient operations.
5.3 Growth in Micro-Fulfillment Centers
Micro-fulfillment centers will increasingly rely on automation to meet urban logistics needs:
Small-Scale Automation for Urban Logistics:
Micro-fulfillment centers will adopt automation to cater to last-mile delivery demands and enable same-day or next-day shipping.
Use of Robotics in Small Warehouses:
Even smaller, decentralized warehouses will incorporate robotics to optimize space utilization and speed up operations.
Conclusion
Automation and robotics are revolutionizing warehousing by addressing labor shortages, enhancing operational efficiency, and meeting evolving customer expectations. Technologies like AGVs, robotics, and AS/RS are helping companies handle higher volumes with greater speed and accuracy while optimizing the use of warehouse space. Although the implementation of automation involves challenges, such as high costs and integration complexities, the long-term benefits of increased productivity and accuracy make it a worthwhile investment. As AI, collaborative robotics, and micro-fulfillment centers continue to shape the future of warehouse automation, companies that embrace these technologies will be well-positioned for success.
Key Takeaways:
Automation provides significant gains in efficiency, accuracy, and space optimization.
Initial costs and integration challenges should be carefully managed to maximize ROI.
Future trends in AI and collaborative robotics will drive the next wave of warehouse automation advancements.
Call to Action (CTA): Share your experiences with warehouse automation and let us know how your organization is leveraging robotics and automation to improve efficiency.
Warehousing automation is transforming logistics with technologies like AGVs, robotics, and AS/RS. Learn how these solutions address labor shortages, enhance efficiency, and prepare companies for the future.
As the logistics industry faces ongoing labor shortages and rising demand, companies are increasingly turning to automation and robotics to enhance warehouse operations. Automation technologies, such as automated guided vehicles (AGVs), robotics, and automated storage and retrieval systems (AS/RS), enable companies to manage higher volumes with fewer workers while maintaining operational speed and accuracy. These technologies not only optimize processes but also help businesses meet evolving customer expectations for rapid delivery and error-free order fulfillment.
This article explores the role of automation and robotics in warehousing, detailing the benefits, challenges, and future trends in this transformative area of logistics.
The Need for Automation in Warehousing
1.1 Combating Labor Shortages
The logistics sector is grappling with a significant labor shortage that is impacting warehousing operations:
Labor Market Challenges:
The logistics industry has struggled to attract and retain workers due to the physically demanding nature of warehouse jobs and competitive hiring pressures.
High turnover rates and an aging workforce further exacerbate the challenge of filling warehousing positions, especially during peak seasons.
Increasing Wage Costs:
Wage inflation and competitive hiring incentives are driving up labor costs, prompting companies to seek cost-effective automation solutions.
Automation reduces dependency on manual labor, helping to mitigate the financial impact of rising wages.
1.2 Managing Higher Volumes and Customer Expectations
Automation is not only a response to labor shortages but also a solution to meet the demands of a rapidly evolving market:
Growth of E-commerce:
The surge in e-commerce has increased pressure on warehouses to handle larger volumes of orders with shorter fulfillment times.
Seasonal peaks, such as Black Friday and holiday shopping, demand flexible and scalable warehouse operations to meet heightened customer expectations.
Need for Speed and Accuracy:
Customers expect same-day or next-day delivery, making speed and precision critical factors in order fulfillment.
Automated systems enhance efficiency by performing repetitive tasks more quickly and accurately than human workers.
Key Automation Technologies in Warehousing
2.1 Automated Guided Vehicles (AGVs)
AGVs are among the most widely used automation technologies in warehouses, offering flexibility and efficiency in material handling:
Overview of AGVs:
AGVs are self-driving vehicles that navigate warehouse floors using sensors, cameras, and pre-programmed routes to transport goods.
These vehicles can operate autonomously or be programmed to follow designated paths, reducing the need for human intervention.
Types of AGVs in Warehousing:
Tugger AGVs: Designed to pull carts or trailers, often used for moving large quantities of goods between different areas.
Unit Load AGVs: Suitable for transporting pallets, bins, or containers; ideal for high-throughput environments.
Forklift AGVs: Automate the lifting and stacking of pallets, offering a safer alternative to traditional manual forklifts.
Benefits of AGVs:
Reduced labor costs: AGVs automate repetitive tasks, allowing companies to reallocate workers to more complex roles.
Increased safety: Automated vehicles reduce the risk of workplace accidents associated with manual material handling.
Scalability: AGVs can be easily added or removed based on demand, making them suitable for warehouses of various sizes.
2.2 Robotics and Robotic Process Automation (RPA)
Robotics and RPA are transforming warehousing by automating complex and repetitive tasks:
Types of Robotics Used in Warehousing:
Collaborative robots (cobots): Work alongside human workers to assist with tasks such as order picking, packing, and sorting.
Sorting robots: Used to pick and place items in the correct locations, streamlining sorting processes in distribution centers.
Palletizing robots: Automate the stacking and organizing of goods on pallets, increasing efficiency in loading and unloading.
Applications of RPA in Warehousing:
Automating data entry: RPA can handle repetitive administrative tasks such as inventory tracking, order processing, and shipment scheduling.
Enhancing workflow efficiency: RPA helps streamline warehouse management processes by integrating with existing warehouse management systems (WMS).
2.3 Automated Storage and Retrieval Systems (AS/RS)
AS/RS technology is essential for maximizing warehouse storage efficiency and optimizing inventory management:
What Is AS/RS?:
AS/RS are computer-controlled systems that automatically place and retrieve goods from storage locations. These systems are often used in conjunction with other automation technologies for a fully integrated approach.
Types of AS/RS:
Mini-load AS/RS: Designed for handling smaller items such as boxes, bins, and cartons.
Unit-load AS/RS: Suitable for storing large and heavy items, typically on pallets.
Shuttle systems: Use automated shuttles to move goods within high-density storage racks, providing quick access to items.
Advantages of AS/RS:
Increased storage capacity: AS/RS allows for vertical stacking, optimizing the use of available space and enabling high-density storage configurations.
Faster retrieval times: Automated systems reduce the time needed to locate and retrieve items, improving order fulfillment speed.
Benefits of Automation and Robotics in Warehousing
3.1 Increased Efficiency and Productivity
Automation allows warehouses to operate more efficiently, even with fewer workers:
Optimizing Material Handling:
Automated systems streamline the movement of goods throughout the warehouse, reducing handling times and minimizing bottlenecks.
Consistent Performance:
Unlike human workers, machines do not experience fatigue or performance fluctuations, ensuring a steady rate of productivity throughout the day.
3.2 Enhanced Accuracy and Reduced Errors
Automation improves order accuracy and reduces the risk of mistakes:
Minimizing Human Error:
Automated picking and sorting systems are programmed to perform tasks precisely, reducing the likelihood of errors.
Improved Quality Control:
Robots can be used to inspect products for defects or discrepancies, ensuring consistent quality in order fulfillment.
3.3 Better Use of Space
Automation helps companies optimize warehouse layouts and maximize storage capacity:
Maximizing Storage Capacity:
AS/RS and other high-density storage solutions make better use of vertical space, allowing warehouses to store more inventory in a smaller footprint.
Flexible Warehouse Layouts:
Automated systems enable more adaptable warehouse designs, allowing facilities to be quickly reconfigured in response to changing operational needs.
Challenges and Considerations in Implementing Automation
4.1 High Initial Investment Costs
The cost of automation is a significant barrier for many companies:
Capital Expenditure for Equipment:
The upfront cost of acquiring AGVs, robotics, and AS/RS can be substantial, particularly for small and medium-sized businesses.
Infrastructure Upgrades:
Existing warehouses may require upgrades to support automation, such as installing power lines, enhancing network connectivity, or reinforcing floors.
4.2 Integration with Existing Systems
Integrating new automation technologies with legacy systems can be challenging:
Compatibility Issues:
New automation solutions may not be easily compatible with older warehouse management systems (WMS), requiring customization or upgrades.
Training Requirements:
Employees need to be trained to operate, monitor, and maintain the new automated systems, which may involve a learning curve.
4.3 Workforce Implications
While automation can reduce the need for manual labor, it also affects the workforce:
Impact on Employment:
Concerns about job displacement arise as manual tasks are automated. Companies need to manage the transition carefully to avoid negative impacts on employees.
Upskilling Opportunities:
Automation creates new roles in areas such as robot maintenance, programming, and data analysis. Companies should invest in training programs to help workers develop these skills.
Future Trends in Warehouse Automation
5.1 Increased Adoption of AI and Machine Learning
AI and machine learning will continue to drive advancements in warehouse automation:
AI-Powered Predictive Analytics:
AI can be used for demand forecasting, optimizing inventory levels, and conducting predictive maintenance on equipment.
Robots with Advanced AI Capabilities:
Robots will increasingly be equipped with AI that allows them to learn, adapt, and perform more complex tasks.
5.2 Expansion of Collaborative Robotics
The use of collaborative robots (cobots) in warehouses is expected to grow:
Rise of Cobots:
More warehouses will integrate cobots to assist human workers with tasks such as lifting, picking, and sorting, especially in environments where human dexterity is required.
Human-Robot Collaboration Models:
New collaboration models will emerge, leveraging the strengths of both human workers and robots for more efficient operations.
5.3 Growth in Micro-Fulfillment Centers
Micro-fulfillment centers will increasingly rely on automation to meet urban logistics needs:
Small-Scale Automation for Urban Logistics:
Micro-fulfillment centers will adopt automation to cater to last-mile delivery demands and enable same-day or next-day shipping.
Use of Robotics in Small Warehouses:
Even smaller, decentralized warehouses will incorporate robotics to optimize space utilization and speed up operations.
Conclusion
Automation and robotics are revolutionizing warehousing by addressing labor shortages, enhancing operational efficiency, and meeting evolving customer expectations. Technologies like AGVs, robotics, and AS/RS are helping companies handle higher volumes with greater speed and accuracy while optimizing the use of warehouse space. Although the implementation of automation involves challenges, such as high costs and integration complexities, the long-term benefits of increased productivity and accuracy make it a worthwhile investment. As AI, collaborative robotics, and micro-fulfillment centers continue to shape the future of warehouse automation, companies that embrace these technologies will be well-positioned for success.
Key Takeaways:
Automation provides significant gains in efficiency, accuracy, and space optimization.
Initial costs and integration challenges should be carefully managed to maximize ROI.
Future trends in AI and collaborative robotics will drive the next wave of warehouse automation advancements.
Call to Action (CTA): Share your experiences with warehouse automation and let us know how your organization is leveraging robotics and automation to improve efficiency.
Other Blogs
Other Blogs
Check our other project Blogs with useful insight and information for your businesses
Other Blogs
Other Blogs
Check our other project Blogs with useful insight and information for your businesses
Other Blogs
Other Blogs
Check our other project Blogs with useful insight and information for your businesses