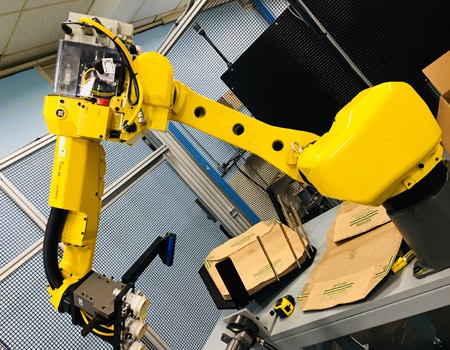
Insights
December 12, 2024
Revolutionizing Logistics: Japan's First Automated Picking Solution Transforms Efficiency at Kirin Group's Ebina Center
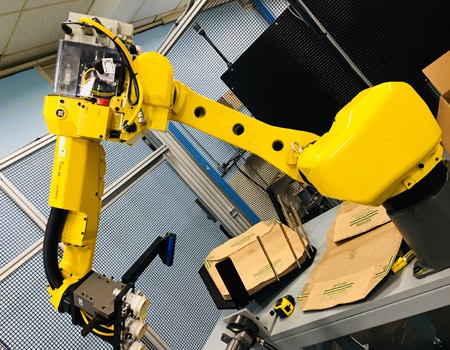
Insights
December 12, 2024
Revolutionizing Logistics: Japan's First Automated Picking Solution Transforms Efficiency at Kirin Group's Ebina Center
Discover how automation is revolutionizing Japan's logistics industry as Kirin Group integrates the country's first automated picking solution at their Ebina distribution center. Learn about its transformative impact on operational efficiency and what it means for the future of supply chain management.
Japan has long been recognized as a leader in technological innovation, from robotics to artificial intelligence, with advancements that reshape entire industries. The logistics sector, critical to keeping global supply chains running smoothly, is no exception. In recent years, automation has become the centerpiece of logistics transformation around the world, and Japan is now setting a new benchmark in this domain. Kirin Group, one of the country’s leading beverage and pharmaceutical giants, has implemented Japan’s first automated picking solution at its Ebina distribution center. This revolutionary adaptation not only enhances operational efficiency but also signals a massive shift in how logistics will be handled in the future.
Logistics forms the backbone of any economy, facilitating the movement of goods from manufacturers to retailers and finally to consumers. As supply chains grow more complex due to increased globalization, the demand for faster, smarter, and more flexible solutions has never been greater. In Japan, where an aging workforce exerts upward pressure on operational costs and labor shortages are becoming an existential challenge, automation is no longer a luxury but a necessity. Kirin Group’s adoption of an automated picking system addresses these challenges head-on, offering a new model for efficiency and scalability.
The Ebina distribution center, located in Kanagawa Prefecture, serves as a hub for Kirin Group's beverage operations, handling everything from storage to delivery. Traditional picking systems, reliant on manual labor, were becoming less sustainable as demand increased and labor availability decreased. The automated picking solution introduced at Ebina represents a sophisticated amalgamation of robotics, artificial intelligence, and data analytics to achieve unprecedented efficiencies. The initiative is a collaboration between Kirin Group and market-leading automation technology providers, showcasing the potential of public-private partnerships in driving industrial innovation.
The heart of the system is an advanced robotic picking arm, capable of identifying, selecting, and sorting products with pinpoint precision. Unlike human workers, who are limited by physical constraints such as fatigue or shift hours, the robotic arm can operate around the clock without compromise. An integrated AI system continuously learns and improves its picking algorithms, ensuring greater accuracy with each iteration. In the fast-paced world of beverage logistics, where mispicks or delays can disrupt entire supply chains, this level of accuracy is a game-changer.
A key feature of the automated picking system is its integration with warehouse management software (WMS). This software tracks inventory, analyzes demand, and orchestrates the movements of both humans and machines in real time. The WMS allows the robotic picking arm to prioritize high-demand items while still maintaining flexibility for unexpected orders. Such dynamic adaptability enhances not only operational efficiency but also customer satisfaction, as retailers can count on consistent and timely deliveries.
One of the most striking impacts of this new automated solution is its measurable efficiency gains. Reports from the Kirin Ebina center indicate a significant reduction in order processing times, enabling faster deliveries to distribution channels. Additionally, the system has drastically reduced picking errors, which traditionally result in costly product returns and customer dissatisfaction. These improvements have a compounding effect, as faster, more accurate operations create a ripple of benefits downstream in the supply chain, from reduced inventory backlogs to enhanced retailer confidence.
Another critical benefit lies in the system’s resilience and scalability. The adoption of automation mitigates risks associated with labor shortages, a particularly acute issue in Japan, where the aging population is causing an unprecedented workforce decline. Automated systems not only fill the gaps left by a shrinking pool of eligible workers but also offer scalability, enabling the company to quickly respond to seasonal demand spikes or market fluctuations. This resilience is particularly vital for companies like Kirin, which operate in a highly competitive and customer-centric industry.
While the operational and economic benefits of automation are evident, its human impact deserves equal attention. Automation often conjures fears of workforce displacement, but Kirin Group has approached this transition thoughtfully. The introduction of automated picking solutions has been accompanied by comprehensive reskilling programs designed to equip employees for roles in oversight, maintenance, and system optimization. In doing so, Kirin ensures that automation supplements rather than supplants human labor, fostering a collaborative environment where workers and machines coexist to achieve greater efficiency.
Kirin Group’s pioneering venture into automated picking solutions is not just a milestone for the company but also a blueprint for the broader logistics sector. The success of the Ebina center underscores the feasibility of adopting cutting-edge technology at scale, even in industries traditionally reliant on manual labor. As global supply chains become increasingly interconnected and customer expectations continue to rise, automated logistics systems will likely transition from niche innovations to industry standards.
The implications of Kirin’s leap into automation extend well beyond Japan. For logistics executives and supply chain managers worldwide, it offers valuable insights into the potential of robotics and AI to drive efficiencies while mitigating risks. By delivering a tangible case study, Kirin inspires other companies to overcome the initial hesitations commonly associated with investing in automation, such as high costs and integration challenges.
For industry leaders considering similar initiatives, the lessons from Kirin’s journey are invaluable. First and foremost, the importance of collaborative partnerships cannot be overstated. By working closely with leading automation technology providers, Kirin ensured that its solution was not only innovative but also tailored to meet the company’s specific operational needs. Secondly, change management plays a pivotal role in the successful implementation of such transformative systems. By prioritizing employee training and maintaining transparent communication throughout the transition, Kirin effectively mitigated resistance and gained organizational buy-in.
As we look ahead, the future of automated logistics appears promising yet complex. Advancements in AI, cloud computing, and Internet of Things (IoT) technologies will likely amplify the capabilities of systems like those at the Ebina center. However, such advancements will also bring challenges, from cybersecurity risks to ethical considerations surrounding workforce displacement. Companies willing to embrace both the opportunities and challenges of automation will be best positioned to thrive in the next era of logistics.
Kirin Group’s adoption of Japan’s first automated picking solution is more than a technological feat; it represents a transformative shift in how logistics will operate in the years to come. Situated at the intersection of necessity and innovation, the Ebina center offers a compelling illustration of how automation can solve modern supply chain challenges while setting new benchmarks for efficiency and resilience. In doing so, it challenges industry leaders to rethink traditional paradigms and pursue bold, forward-looking strategies.
The logistics industry is on the cusp of a revolution, and Kirin Group has firmly positioned itself at the forefront. As the world takes notice of what is happening at the Ebina center, the ripple effect will encourage other companies to harness technology’s full potential. Whether it is to meet rising consumer expectations, navigate workforce challenges, or simply remain competitive in a dynamic market, the path forward is becoming increasingly clear: embrace automation not just as a tool for efficiency but as a cornerstone for future growth. As Kirin Group has shown, those who adapt boldly and strategically will define success in this new era of logistics.
Japan has long been recognized as a leader in technological innovation, from robotics to artificial intelligence, with advancements that reshape entire industries. The logistics sector, critical to keeping global supply chains running smoothly, is no exception. In recent years, automation has become the centerpiece of logistics transformation around the world, and Japan is now setting a new benchmark in this domain. Kirin Group, one of the country’s leading beverage and pharmaceutical giants, has implemented Japan’s first automated picking solution at its Ebina distribution center. This revolutionary adaptation not only enhances operational efficiency but also signals a massive shift in how logistics will be handled in the future.
Logistics forms the backbone of any economy, facilitating the movement of goods from manufacturers to retailers and finally to consumers. As supply chains grow more complex due to increased globalization, the demand for faster, smarter, and more flexible solutions has never been greater. In Japan, where an aging workforce exerts upward pressure on operational costs and labor shortages are becoming an existential challenge, automation is no longer a luxury but a necessity. Kirin Group’s adoption of an automated picking system addresses these challenges head-on, offering a new model for efficiency and scalability.
The Ebina distribution center, located in Kanagawa Prefecture, serves as a hub for Kirin Group's beverage operations, handling everything from storage to delivery. Traditional picking systems, reliant on manual labor, were becoming less sustainable as demand increased and labor availability decreased. The automated picking solution introduced at Ebina represents a sophisticated amalgamation of robotics, artificial intelligence, and data analytics to achieve unprecedented efficiencies. The initiative is a collaboration between Kirin Group and market-leading automation technology providers, showcasing the potential of public-private partnerships in driving industrial innovation.
The heart of the system is an advanced robotic picking arm, capable of identifying, selecting, and sorting products with pinpoint precision. Unlike human workers, who are limited by physical constraints such as fatigue or shift hours, the robotic arm can operate around the clock without compromise. An integrated AI system continuously learns and improves its picking algorithms, ensuring greater accuracy with each iteration. In the fast-paced world of beverage logistics, where mispicks or delays can disrupt entire supply chains, this level of accuracy is a game-changer.
A key feature of the automated picking system is its integration with warehouse management software (WMS). This software tracks inventory, analyzes demand, and orchestrates the movements of both humans and machines in real time. The WMS allows the robotic picking arm to prioritize high-demand items while still maintaining flexibility for unexpected orders. Such dynamic adaptability enhances not only operational efficiency but also customer satisfaction, as retailers can count on consistent and timely deliveries.
One of the most striking impacts of this new automated solution is its measurable efficiency gains. Reports from the Kirin Ebina center indicate a significant reduction in order processing times, enabling faster deliveries to distribution channels. Additionally, the system has drastically reduced picking errors, which traditionally result in costly product returns and customer dissatisfaction. These improvements have a compounding effect, as faster, more accurate operations create a ripple of benefits downstream in the supply chain, from reduced inventory backlogs to enhanced retailer confidence.
Another critical benefit lies in the system’s resilience and scalability. The adoption of automation mitigates risks associated with labor shortages, a particularly acute issue in Japan, where the aging population is causing an unprecedented workforce decline. Automated systems not only fill the gaps left by a shrinking pool of eligible workers but also offer scalability, enabling the company to quickly respond to seasonal demand spikes or market fluctuations. This resilience is particularly vital for companies like Kirin, which operate in a highly competitive and customer-centric industry.
While the operational and economic benefits of automation are evident, its human impact deserves equal attention. Automation often conjures fears of workforce displacement, but Kirin Group has approached this transition thoughtfully. The introduction of automated picking solutions has been accompanied by comprehensive reskilling programs designed to equip employees for roles in oversight, maintenance, and system optimization. In doing so, Kirin ensures that automation supplements rather than supplants human labor, fostering a collaborative environment where workers and machines coexist to achieve greater efficiency.
Kirin Group’s pioneering venture into automated picking solutions is not just a milestone for the company but also a blueprint for the broader logistics sector. The success of the Ebina center underscores the feasibility of adopting cutting-edge technology at scale, even in industries traditionally reliant on manual labor. As global supply chains become increasingly interconnected and customer expectations continue to rise, automated logistics systems will likely transition from niche innovations to industry standards.
The implications of Kirin’s leap into automation extend well beyond Japan. For logistics executives and supply chain managers worldwide, it offers valuable insights into the potential of robotics and AI to drive efficiencies while mitigating risks. By delivering a tangible case study, Kirin inspires other companies to overcome the initial hesitations commonly associated with investing in automation, such as high costs and integration challenges.
For industry leaders considering similar initiatives, the lessons from Kirin’s journey are invaluable. First and foremost, the importance of collaborative partnerships cannot be overstated. By working closely with leading automation technology providers, Kirin ensured that its solution was not only innovative but also tailored to meet the company’s specific operational needs. Secondly, change management plays a pivotal role in the successful implementation of such transformative systems. By prioritizing employee training and maintaining transparent communication throughout the transition, Kirin effectively mitigated resistance and gained organizational buy-in.
As we look ahead, the future of automated logistics appears promising yet complex. Advancements in AI, cloud computing, and Internet of Things (IoT) technologies will likely amplify the capabilities of systems like those at the Ebina center. However, such advancements will also bring challenges, from cybersecurity risks to ethical considerations surrounding workforce displacement. Companies willing to embrace both the opportunities and challenges of automation will be best positioned to thrive in the next era of logistics.
Kirin Group’s adoption of Japan’s first automated picking solution is more than a technological feat; it represents a transformative shift in how logistics will operate in the years to come. Situated at the intersection of necessity and innovation, the Ebina center offers a compelling illustration of how automation can solve modern supply chain challenges while setting new benchmarks for efficiency and resilience. In doing so, it challenges industry leaders to rethink traditional paradigms and pursue bold, forward-looking strategies.
The logistics industry is on the cusp of a revolution, and Kirin Group has firmly positioned itself at the forefront. As the world takes notice of what is happening at the Ebina center, the ripple effect will encourage other companies to harness technology’s full potential. Whether it is to meet rising consumer expectations, navigate workforce challenges, or simply remain competitive in a dynamic market, the path forward is becoming increasingly clear: embrace automation not just as a tool for efficiency but as a cornerstone for future growth. As Kirin Group has shown, those who adapt boldly and strategically will define success in this new era of logistics.
Discover how automation is revolutionizing Japan's logistics industry as Kirin Group integrates the country's first automated picking solution at their Ebina distribution center. Learn about its transformative impact on operational efficiency and what it means for the future of supply chain management.
Japan has long been recognized as a leader in technological innovation, from robotics to artificial intelligence, with advancements that reshape entire industries. The logistics sector, critical to keeping global supply chains running smoothly, is no exception. In recent years, automation has become the centerpiece of logistics transformation around the world, and Japan is now setting a new benchmark in this domain. Kirin Group, one of the country’s leading beverage and pharmaceutical giants, has implemented Japan’s first automated picking solution at its Ebina distribution center. This revolutionary adaptation not only enhances operational efficiency but also signals a massive shift in how logistics will be handled in the future.
Logistics forms the backbone of any economy, facilitating the movement of goods from manufacturers to retailers and finally to consumers. As supply chains grow more complex due to increased globalization, the demand for faster, smarter, and more flexible solutions has never been greater. In Japan, where an aging workforce exerts upward pressure on operational costs and labor shortages are becoming an existential challenge, automation is no longer a luxury but a necessity. Kirin Group’s adoption of an automated picking system addresses these challenges head-on, offering a new model for efficiency and scalability.
The Ebina distribution center, located in Kanagawa Prefecture, serves as a hub for Kirin Group's beverage operations, handling everything from storage to delivery. Traditional picking systems, reliant on manual labor, were becoming less sustainable as demand increased and labor availability decreased. The automated picking solution introduced at Ebina represents a sophisticated amalgamation of robotics, artificial intelligence, and data analytics to achieve unprecedented efficiencies. The initiative is a collaboration between Kirin Group and market-leading automation technology providers, showcasing the potential of public-private partnerships in driving industrial innovation.
The heart of the system is an advanced robotic picking arm, capable of identifying, selecting, and sorting products with pinpoint precision. Unlike human workers, who are limited by physical constraints such as fatigue or shift hours, the robotic arm can operate around the clock without compromise. An integrated AI system continuously learns and improves its picking algorithms, ensuring greater accuracy with each iteration. In the fast-paced world of beverage logistics, where mispicks or delays can disrupt entire supply chains, this level of accuracy is a game-changer.
A key feature of the automated picking system is its integration with warehouse management software (WMS). This software tracks inventory, analyzes demand, and orchestrates the movements of both humans and machines in real time. The WMS allows the robotic picking arm to prioritize high-demand items while still maintaining flexibility for unexpected orders. Such dynamic adaptability enhances not only operational efficiency but also customer satisfaction, as retailers can count on consistent and timely deliveries.
One of the most striking impacts of this new automated solution is its measurable efficiency gains. Reports from the Kirin Ebina center indicate a significant reduction in order processing times, enabling faster deliveries to distribution channels. Additionally, the system has drastically reduced picking errors, which traditionally result in costly product returns and customer dissatisfaction. These improvements have a compounding effect, as faster, more accurate operations create a ripple of benefits downstream in the supply chain, from reduced inventory backlogs to enhanced retailer confidence.
Another critical benefit lies in the system’s resilience and scalability. The adoption of automation mitigates risks associated with labor shortages, a particularly acute issue in Japan, where the aging population is causing an unprecedented workforce decline. Automated systems not only fill the gaps left by a shrinking pool of eligible workers but also offer scalability, enabling the company to quickly respond to seasonal demand spikes or market fluctuations. This resilience is particularly vital for companies like Kirin, which operate in a highly competitive and customer-centric industry.
While the operational and economic benefits of automation are evident, its human impact deserves equal attention. Automation often conjures fears of workforce displacement, but Kirin Group has approached this transition thoughtfully. The introduction of automated picking solutions has been accompanied by comprehensive reskilling programs designed to equip employees for roles in oversight, maintenance, and system optimization. In doing so, Kirin ensures that automation supplements rather than supplants human labor, fostering a collaborative environment where workers and machines coexist to achieve greater efficiency.
Kirin Group’s pioneering venture into automated picking solutions is not just a milestone for the company but also a blueprint for the broader logistics sector. The success of the Ebina center underscores the feasibility of adopting cutting-edge technology at scale, even in industries traditionally reliant on manual labor. As global supply chains become increasingly interconnected and customer expectations continue to rise, automated logistics systems will likely transition from niche innovations to industry standards.
The implications of Kirin’s leap into automation extend well beyond Japan. For logistics executives and supply chain managers worldwide, it offers valuable insights into the potential of robotics and AI to drive efficiencies while mitigating risks. By delivering a tangible case study, Kirin inspires other companies to overcome the initial hesitations commonly associated with investing in automation, such as high costs and integration challenges.
For industry leaders considering similar initiatives, the lessons from Kirin’s journey are invaluable. First and foremost, the importance of collaborative partnerships cannot be overstated. By working closely with leading automation technology providers, Kirin ensured that its solution was not only innovative but also tailored to meet the company’s specific operational needs. Secondly, change management plays a pivotal role in the successful implementation of such transformative systems. By prioritizing employee training and maintaining transparent communication throughout the transition, Kirin effectively mitigated resistance and gained organizational buy-in.
As we look ahead, the future of automated logistics appears promising yet complex. Advancements in AI, cloud computing, and Internet of Things (IoT) technologies will likely amplify the capabilities of systems like those at the Ebina center. However, such advancements will also bring challenges, from cybersecurity risks to ethical considerations surrounding workforce displacement. Companies willing to embrace both the opportunities and challenges of automation will be best positioned to thrive in the next era of logistics.
Kirin Group’s adoption of Japan’s first automated picking solution is more than a technological feat; it represents a transformative shift in how logistics will operate in the years to come. Situated at the intersection of necessity and innovation, the Ebina center offers a compelling illustration of how automation can solve modern supply chain challenges while setting new benchmarks for efficiency and resilience. In doing so, it challenges industry leaders to rethink traditional paradigms and pursue bold, forward-looking strategies.
The logistics industry is on the cusp of a revolution, and Kirin Group has firmly positioned itself at the forefront. As the world takes notice of what is happening at the Ebina center, the ripple effect will encourage other companies to harness technology’s full potential. Whether it is to meet rising consumer expectations, navigate workforce challenges, or simply remain competitive in a dynamic market, the path forward is becoming increasingly clear: embrace automation not just as a tool for efficiency but as a cornerstone for future growth. As Kirin Group has shown, those who adapt boldly and strategically will define success in this new era of logistics.
Other Blogs
Other Blogs
Check our other project Blogs with useful insight and information for your businesses
Other Blogs
Other Blogs
Check our other project Blogs with useful insight and information for your businesses
Other Blogs
Other Blogs
Check our other project Blogs with useful insight and information for your businesses